Products
Solutions
Resources
9977 N 90th Street, Suite 250 Scottsdale, AZ 85258 | 1-800-637-7496
© 2024 InEight, Inc. All Rights Reserved | Privacy Statement | Terms of Service | Cookie Policy | Do not sell/share my information
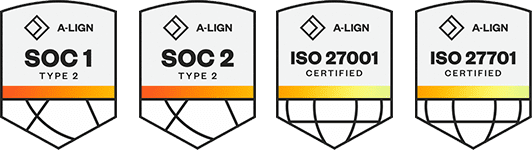
Cost Item Assemblies utilize predictive models to quickly and accurately estimate elements of a job that can be repetitive in nature on a single job or from job to job. They use parameter driven estimating to create cost items. They use created parameters and mathematical calculations to incorporate quantity takeoffs and estimate quantification into cost items. A cost item assembly will output fully populated cost items directly into the project CBS. The inputs are dimension values and specification sections, while the output is cost items.
Cost Item Assemblies accomplish the following:
Model a construction system or component that is quick and easy to employ
Promote a consistent process of estimating among various users
Enable less experienced users to more efficiently create an estimate
Provide good visibility into the assumptions and calculations made to obtain the results
Provide the flexibility to easily adjust model assumptions and account for varying project requirements from estimate to estimate
All the following can be done with Cost Item Assemblies:
Assembly employments can be re-opened to modify inputs
Assemblies can be stored in the Library and imported like resources
Assemblies can be copied and pasted between projects
Assemblies can be created from existing project cost items
Assemblies can be modified for project specific needs
Assemblies can be modified and employments updated in the project
Employed assemblies can become permanent cost items by deleting the link
Assemblies can be created for either metrical or imperial units
There are typically two types of users that work with Cost Item Assemblies:
The power user, someone like the lead estimator, creates the cost item assemblies
The end user uses the created assemblies
User |
Function |
---|---|
Power User |
This user can determine what questions need to be answered to create a standard construction system, and how specifically to use those answers in determining the systems quantities, cost and resources to be applied in the estimate. Many companies have spreadsheets that they have created for estimators in the organization to use in estimating specific types of work. If you are the person that often creates or enhances those spreadsheets, you probably fall into the category of being a user that will create Cost Item Assemblies. |
End User |
This is sometimes a less experienced estimator that will benefit from being provided a set of questions to answer because it can help the estimator develop an understanding for the way the work is estimated and provide them with guidance in gathering the right information. The use of Cost Item Assemblies is not exclusive to less experienced estimators, however. They can be used by anyone involved in the estimating process that wants to quickly create an estimate for a scope of work in a consistent and repeatable way. Cost Item Assemblies can be a great way to initialize an estimate and give the estimator more time to focus on analyzing the job and considering different ways of approaching the work. |
The use of data blocks in the Cost Item Assembly Register allows you to set up a layout that works best for you.
The data blocks in the Cost Item Assembly Record are:
Cost Items
Inputs
Calculations
Notes
Setup
Tables
Sub Assemblies
The Default Data Block view looks like the following:
To move Calculations onto the screen, simply click on the name and drag it until the following options appear:
Next, choose where to place it on your screen:
The calculations data block now appears on the screen.
To look at Setup and Tables, click on the tabs to view them.
To get rid of the Notes screen, simply press the X, and to bring it back, click on Default Data Blocks in the ribbon.
Additional Information
9977 N 90th Street, Suite 250 Scottsdale, AZ 85258 | 1-800-637-7496
© 2024 InEight, Inc. All Rights Reserved | Privacy Statement | Terms of Service | Cookie Policy | Do not sell/share my information